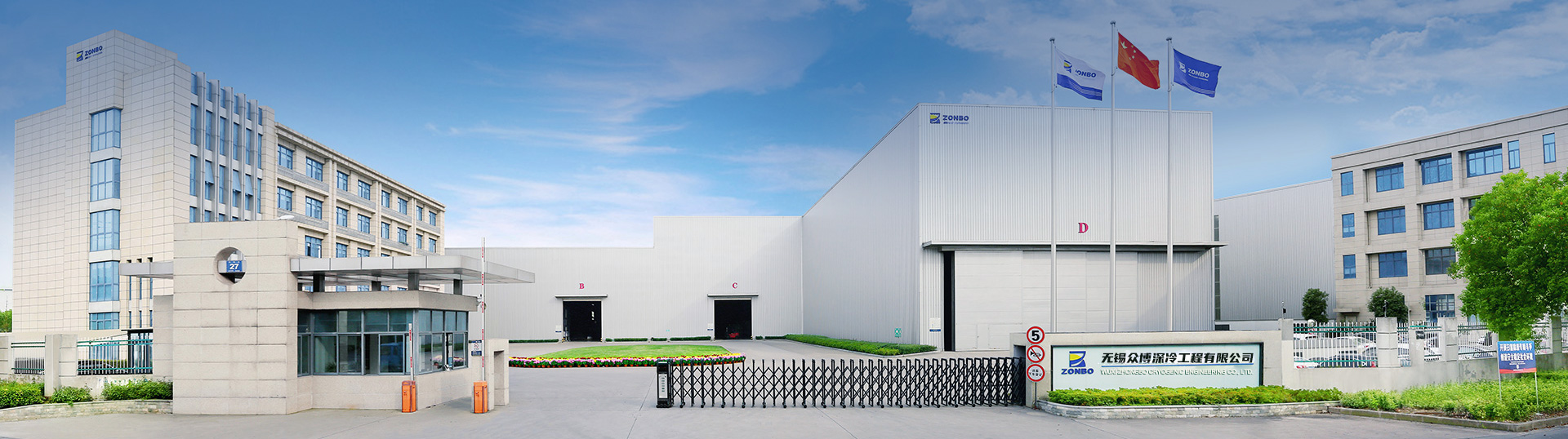
ABOUT
What are the design points of the main frame of a shell and tube heat exchanger
The main framework design of a shell and tube heat exchanger needs to take into account structural strength, thermal expansion compensation, fluid distribution, and sealing reliability. The following are the core design points:
1. Key points of shell design
Materials and pressure resistance
The shell is usually made of high-strength and corrosion-resistant materials (such as carbon steel and stainless steel), which need to meet the requirements of process pressure (usually 0.1-10MPa) and temperature (below 400 ℃).
The wall thickness needs to be optimized through finite element analysis to ensure that no deformation occurs under high temperature and high pressure.
structural style
Cylindrical design: equipped with elliptical or disc-shaped heads at both ends to ensure stable internal pressure.
Manhole and handhole: Set up maintenance interfaces (diameter ≥ 400mm) for internal inspection and cleaning.
Stress compensation
Thermal expansion treatment: For fixed tube plate heat exchangers, it is necessary to verify the thermal stress caused by the temperature difference between the shell and the tube bundle, and if necessary, install expansion joints.
Longitudinal partition: Install longitudinal partitions to prevent fluid short circuits when the flow rate of the shell side medium is low.
2. Key points of bundle design
Specification and arrangement of heat exchange tubes
Pipe diameter and wall thickness: commonly used outer diameter is 12-25mm, wall thickness is 1.5-3mm, and the material is mostly 304/316L stainless steel.
Arrangement method: equilateral triangle arrangement (high heat transfer efficiency) or square arrangement (easy to clean), with a pipe spacing of 1.25-1.5 times the pipe diameter.
Enhanced heat transfer: using threaded pipes, corrugated pipes, or internally inserted turbulence elements (such as spiral ties).
Tube plate design
Material and thickness: Thick steel plates (thickness ≥ 20mm) are used, and high-quality materials are required for corrosion-resistant media.
Connection method: Strength expansion joint (pressure ≤ 10MPa) or hydraulic expansion joint (pressure ≤ 30MPa), and the weld seam must pass penetration testing (PT) to ensure zero defects.
Split range design: The fluid inside the tube is divided into stages through split range baffles, with approximately equal numbers of tubes in each stage, simple form, and few welds.
Number of tube side and shell side
Number of passes: Choose 1, 2, 4, or 6 passes based on flow rate and heat transfer area requirements to avoid excessive passes leading to increased fluid resistance.
Number of shell passes: Multiple shell passes are achieved by setting longitudinal partitions to improve heat transfer efficiency.
3. Head and fluid distribution design
Head type and function
Fixed tube plate: Welding the head and tube plate, suitable for working conditions with a temperature difference of ≤ 50 ℃.
Floating head type: One end of the head can float, suitable for situations with a temperature difference of 100-150 ℃.
U-shaped tube type: The heat exchange tube is bent into a U-shape, allowing for axial thermal expansion and suitable for extreme working conditions with a temperature difference greater than 150 ℃.
Flow diversion design: Flow deflectors (such as bow shaped baffles) are installed inside the head to evenly distribute the fluid to each heat exchange tube and avoid flow deviation.
Optimization of fluid flow path
Flow space selection:
Piping: Suitable for unclean, scaling prone, corrosive, high-pressure fluids.
Shell side: Suitable for fluids with saturated steam, high viscosity, or low flow rate.
Flow rate control: Increasing the flow rate can improve the convective heat transfer coefficient, but it requires balancing fluid resistance and power consumption.
4. Sealing and support design
Sealing structure
Tube side sealing: achieved through mechanical expansion or hydraulic expansion.
Shell side seal:
Fixed tube plate: The shell is welded to the tube plate without dynamic sealing.
Floating head type: using packing seal (graphite packing) or mechanical seal (temperature resistant to 350 ℃).
U-shaped tube type: sealed with gaskets (commonly metal wrapped gaskets), with a temperature resistance range of -200 ℃ to 800 ℃.
Support and anti vibration design
Pull rod and distance tube: The diameter of the pull rod is 10-20mm, and the length error of the distance tube is ≤± 0.5mm, ensuring consistent spacing between the baffle plates.
Anti vibration measures:
Misalignment of baffle notches: Adjacent baffle notches rotate 90 °, disrupting fluid resonance frequency.
Damper: Install rubber damping blocks at the free end of the tube bundle to reduce vibration amplitude (≤ 0.1mm).
5. Strength and reliability design
Stress Calculation and Verification
For high temperature and high pressure working conditions, stress calculation is required to ensure the safety of compressed components.
Using domestically produced standard materials and components, calculate or verify according to the safety technical regulations for pressure vessels.
Corrosion resistant and wear-resistant design
Material selection: Corrosion resistant materials (such as titanium and Hastelloy) should be selected for corrosive media.
Surface treatment: Hardening or coating wear-resistant parts with wear-resistant coatings.
Maintainability design
Detachable structure: The head, pipe box and other components are connected in a detachable manner for easy maintenance and cleaning.
Cleaning port: Set up a cleaning port or use a detachable pipe box design for easy daily inspection and cleaning.
1. Key points of shell design
Materials and pressure resistance
The shell is usually made of high-strength and corrosion-resistant materials (such as carbon steel and stainless steel), which need to meet the requirements of process pressure (usually 0.1-10MPa) and temperature (below 400 ℃).
The wall thickness needs to be optimized through finite element analysis to ensure that no deformation occurs under high temperature and high pressure.
structural style
Cylindrical design: equipped with elliptical or disc-shaped heads at both ends to ensure stable internal pressure.
Manhole and handhole: Set up maintenance interfaces (diameter ≥ 400mm) for internal inspection and cleaning.
Stress compensation
Thermal expansion treatment: For fixed tube plate heat exchangers, it is necessary to verify the thermal stress caused by the temperature difference between the shell and the tube bundle, and if necessary, install expansion joints.
Longitudinal partition: Install longitudinal partitions to prevent fluid short circuits when the flow rate of the shell side medium is low.
2. Key points of bundle design
Specification and arrangement of heat exchange tubes
Pipe diameter and wall thickness: commonly used outer diameter is 12-25mm, wall thickness is 1.5-3mm, and the material is mostly 304/316L stainless steel.
Arrangement method: equilateral triangle arrangement (high heat transfer efficiency) or square arrangement (easy to clean), with a pipe spacing of 1.25-1.5 times the pipe diameter.
Enhanced heat transfer: using threaded pipes, corrugated pipes, or internally inserted turbulence elements (such as spiral ties).
Tube plate design
Material and thickness: Thick steel plates (thickness ≥ 20mm) are used, and high-quality materials are required for corrosion-resistant media.
Connection method: Strength expansion joint (pressure ≤ 10MPa) or hydraulic expansion joint (pressure ≤ 30MPa), and the weld seam must pass penetration testing (PT) to ensure zero defects.
Split range design: The fluid inside the tube is divided into stages through split range baffles, with approximately equal numbers of tubes in each stage, simple form, and few welds.
Number of tube side and shell side
Number of passes: Choose 1, 2, 4, or 6 passes based on flow rate and heat transfer area requirements to avoid excessive passes leading to increased fluid resistance.
Number of shell passes: Multiple shell passes are achieved by setting longitudinal partitions to improve heat transfer efficiency.
3. Head and fluid distribution design
Head type and function
Fixed tube plate: Welding the head and tube plate, suitable for working conditions with a temperature difference of ≤ 50 ℃.
Floating head type: One end of the head can float, suitable for situations with a temperature difference of 100-150 ℃.
U-shaped tube type: The heat exchange tube is bent into a U-shape, allowing for axial thermal expansion and suitable for extreme working conditions with a temperature difference greater than 150 ℃.
Flow diversion design: Flow deflectors (such as bow shaped baffles) are installed inside the head to evenly distribute the fluid to each heat exchange tube and avoid flow deviation.
Optimization of fluid flow path
Flow space selection:
Piping: Suitable for unclean, scaling prone, corrosive, high-pressure fluids.
Shell side: Suitable for fluids with saturated steam, high viscosity, or low flow rate.
Flow rate control: Increasing the flow rate can improve the convective heat transfer coefficient, but it requires balancing fluid resistance and power consumption.
4. Sealing and support design
Sealing structure
Tube side sealing: achieved through mechanical expansion or hydraulic expansion.
Shell side seal:
Fixed tube plate: The shell is welded to the tube plate without dynamic sealing.
Floating head type: using packing seal (graphite packing) or mechanical seal (temperature resistant to 350 ℃).
U-shaped tube type: sealed with gaskets (commonly metal wrapped gaskets), with a temperature resistance range of -200 ℃ to 800 ℃.
Support and anti vibration design
Pull rod and distance tube: The diameter of the pull rod is 10-20mm, and the length error of the distance tube is ≤± 0.5mm, ensuring consistent spacing between the baffle plates.
Anti vibration measures:
Misalignment of baffle notches: Adjacent baffle notches rotate 90 °, disrupting fluid resonance frequency.
Damper: Install rubber damping blocks at the free end of the tube bundle to reduce vibration amplitude (≤ 0.1mm).
5. Strength and reliability design
Stress Calculation and Verification
For high temperature and high pressure working conditions, stress calculation is required to ensure the safety of compressed components.
Using domestically produced standard materials and components, calculate or verify according to the safety technical regulations for pressure vessels.
Corrosion resistant and wear-resistant design
Material selection: Corrosion resistant materials (such as titanium and Hastelloy) should be selected for corrosive media.
Surface treatment: Hardening or coating wear-resistant parts with wear-resistant coatings.
Maintainability design
Detachable structure: The head, pipe box and other components are connected in a detachable manner for easy maintenance and cleaning.
Cleaning port: Set up a cleaning port or use a detachable pipe box design for easy daily inspection and cleaning.
Prev: None