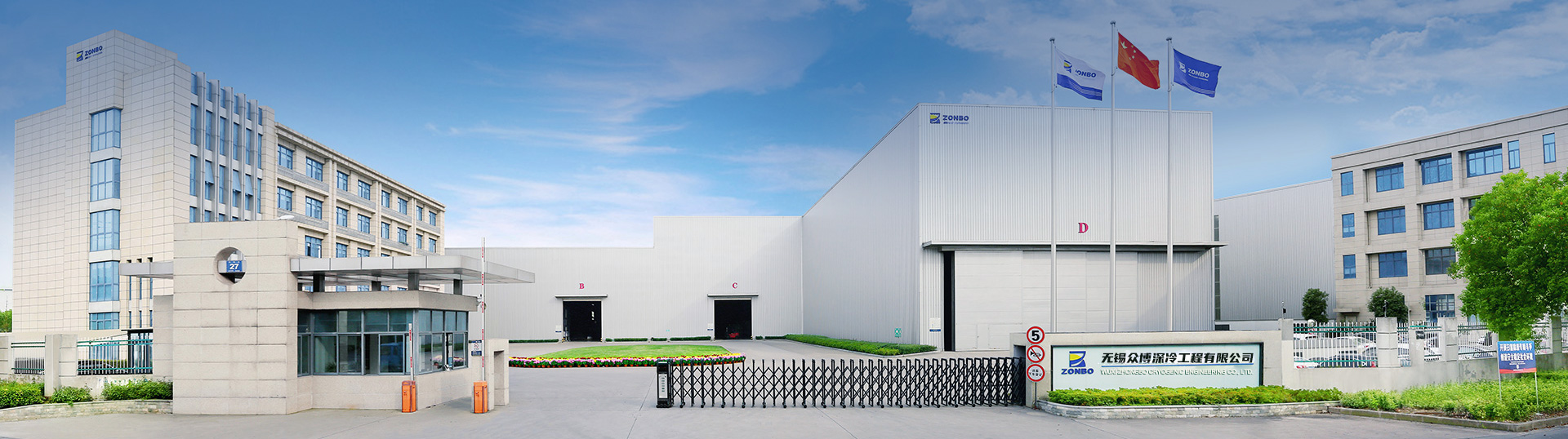
ABOUT
Structural composition of coil-wound heat exchanger
The structural composition of a coil-wound heat exchanger mainly includes the following core components:
Winding core body:
Central tube: As the supporting body of the heat exchange tube, it needs to have sufficient strength and rigidity to ensure that the heat exchange tube remains stable during the winding process.
Heat exchange tube: made of high thermal conductivity materials (such as stainless steel, copper alloy), with a diameter of usually 8-25 millimeters, tightly wound in a spiral form around the central cylinder. Heat exchange tubes can form continuous flow channels through single or multiple tube welding, with lengths up to tens or even hundreds of meters.
Fixed distance components: including flat gaskets, irregular gaskets, and pipe clamps, used to accurately adjust the radial and axial spacing of heat exchange tubes to ensure uniform fluid distribution. The winding direction of adjacent layers is opposite, and the winding angle is generally 3 ° -20 °. The stability of the tube bundle is maintained by distance pieces.
Shell:
Cylinder body: Made of high-strength materials (such as carbon steel or stainless steel), with baffles inside to guide the fluid flow in the shell side and enhance turbulence effect.
Head: Located at both ends of the shell, it adopts a detachable design for easy maintenance, and is equipped with a distributor inside to ensure uniform distribution of fluid in the pipe side. The head and tube plate are connected by flanges to form a closed fluid channel.
Tube plate and supporting structure:
Tube plate: As a connecting component between the heat exchange tube and the shell, it adopts a connection structure of strength welding and adhesive expansion to ensure sealing. The multi stream heat exchanger achieves medium isolation through an integral tube plate structure with partitioned piping.
Supporting structure: Made of high-strength materials, it fixes the tube bundle and shell to prevent vibration or displacement during operation, while also withstanding thermal expansion stress.
Key connection and sealing design:
Welding process: The heat exchange tubes and tube sheets are welded using automated welding technology, with uniform and full welds to avoid the risk of leakage.
Thermal stress compensation: Free sections are designed at both ends of the tube bundle to absorb thermal expansion stress through axial expansion and contraction, reducing the risk of tube plate cracking.
Winding core body:
Central tube: As the supporting body of the heat exchange tube, it needs to have sufficient strength and rigidity to ensure that the heat exchange tube remains stable during the winding process.
Heat exchange tube: made of high thermal conductivity materials (such as stainless steel, copper alloy), with a diameter of usually 8-25 millimeters, tightly wound in a spiral form around the central cylinder. Heat exchange tubes can form continuous flow channels through single or multiple tube welding, with lengths up to tens or even hundreds of meters.
Fixed distance components: including flat gaskets, irregular gaskets, and pipe clamps, used to accurately adjust the radial and axial spacing of heat exchange tubes to ensure uniform fluid distribution. The winding direction of adjacent layers is opposite, and the winding angle is generally 3 ° -20 °. The stability of the tube bundle is maintained by distance pieces.
Shell:
Cylinder body: Made of high-strength materials (such as carbon steel or stainless steel), with baffles inside to guide the fluid flow in the shell side and enhance turbulence effect.
Head: Located at both ends of the shell, it adopts a detachable design for easy maintenance, and is equipped with a distributor inside to ensure uniform distribution of fluid in the pipe side. The head and tube plate are connected by flanges to form a closed fluid channel.
Tube plate and supporting structure:
Tube plate: As a connecting component between the heat exchange tube and the shell, it adopts a connection structure of strength welding and adhesive expansion to ensure sealing. The multi stream heat exchanger achieves medium isolation through an integral tube plate structure with partitioned piping.
Supporting structure: Made of high-strength materials, it fixes the tube bundle and shell to prevent vibration or displacement during operation, while also withstanding thermal expansion stress.
Key connection and sealing design:
Welding process: The heat exchange tubes and tube sheets are welded using automated welding technology, with uniform and full welds to avoid the risk of leakage.
Thermal stress compensation: Free sections are designed at both ends of the tube bundle to absorb thermal expansion stress through axial expansion and contraction, reducing the risk of tube plate cracking.
Prev: None